Виробництво золота – це процес, який цікавить не тільки окремі галузі промисловості, але й цілі держави. Цей благородний метал використовується в стоматології, електроніці, хімічній промисловості, будівництві та ювелірній справі. Золоті злитки й досі застосовуються як частина золотовалютних резервів.
Золото видобувають із золотоносних руд, проте в рудах його мало. Окрім того, залежно від типу руди, золото може бути розсіяним по об’єму та перебувати у складі хімічних сполук разом з іншими металами. З деяких руд екстракція золота за допомогою традиційних технологій практично неможлива. Саме тому нині як ніколи актуальні нестандартні інноваційні технології для видобутку золота.
Види золотоносних руд
Виділяють п’ять основних типів золотоносних руд:
- малосульфідні корінні руди;
- золото-піритові руди;
- сульфідні золото-мідні руди;
- золото-миш’якові руди;
- поліметалічні руди.
Екстракція золота з цих руд може здійснюватися різними методами, залежно від складу, ступеня руйнування та засміченості руди, а також розмірів частинок золота.
Ціанування і флотація
Виробництво золота неможливе без процесів флотації та ціанування. Це базові процеси збагачення золотоносної руди. Ціанування рекомендується для обробки більшості кремнієвих золотих руд, тоді як флотація використовується для видобутку золота з сульфідних руд. Також є руди, для обробки яких застосовуються обидва методи. У цьому випадку вибір методу базується на оптимізації витрат і собівартості кінцевого продукту. Використовуються також комбіновані методи на основі ціанування і флотації.
Процес ціанування у виробництві золота можна умовно поділити на два етапи. На першому етапі золото, що міститься в руді, розчиняється за допомогою ціаніду. Потім розчин відокремлюється, а золото осаджується за допомогою цинку. Встановлено, що дрібне подрібнення руди дає низку переваг, серед яких: скорочення часу обробки, вища екстракція золота та можливість застосування ціанування до складніших руд. Для подрібнення використовуються великогабаритні й енергоємні млини.
Флотація також вимагає тонкого подрібнення золотовмісної руди. Подрібнена руда подається у спеціальну ванну разом із рідиною та реагентами. За допомогою швидкохідної мішалки пульпа змішується з дрібними бульбашками повітря, що сприяє відділенню золотовмісних частинок, які прилипають до бульбашок і піднімаються на поверхню. Далі отриману «золоту» піну зневоднюють, а концентрат відправляють на подальшу переробку.
Виробництво золота методом флотаційного поділу золото-миш’яково-піритових концентратів
Усі методи поділу миш’яково-піритових концентратів базуються на різній окиснюваності поверхні арсенопіриту та піриту під дією окислювальних реагентів. Проте всі реагентні методи мають низку недоліків:
- необхідність суворого дотримання режиму, оскільки навіть найменші зміни можуть призвести до значного погіршення кінцевого результату;
- висока трудомісткість через багаторазові промивки для зняття й видалення колектора з концентрату;
- збільшення витрат реагентів, що потребують подальшої нейтралізації для захисту навколишнього середовища.
Для підвищення ефективності флотаційного процесу рекомендується використовувати апарати вихрового шару (АВС), які можна застосовувати для попередньої обробки руди в сухому вигляді або у вигляді пульпи перед подачею у флотаційну машину.
Що таке апарат вихрового шару і чому він ефективний у видобутку золота?
Апарат вихрового шару застосовується для інтенсифікації багатьох технологічних процесів, диспергування й активації різних речовин. Конструктивно апарат складається з обмотки індуктора, робочої камери з немагнітного матеріалу та феромагнітних частинок певного співвідношення довжини й діаметра, що нагадують голки.
Оброблюваний концентрат подається в робочу камеру апарата, де інтенсивно перемішується феромагнітними частинками, які рухаються по складних траєкторіях під впливом обертового електромагнітного поля. Ці частинки стикаються одна з одною, з частинками концентрату й зі стінками робочої камери, створюючи так званий вихровий шар. Звідси і назва – апарат вихрового шару.
У процесі перемішування частинки концентрату піддаються дії додаткових факторів, що виникають у робочій камері: електричних і магнітних полів, індукційних струмів і їхніх розрядів, акустичних коливань, активації та температури.
Одна з особливостей АВС полягає в тому, що процеси в робочій камері можуть проводитися як періодично, так і безперервно. При цьому феромагнітні частинки не виносяться з робочої камери потоком рідини або газу, а утримуються магнітним полем.
Результати експерименту з обробки флотаційного концентрату у вихровому шарі феромагнітних частинок
Об’єктом дослідження був вибраний флотаційний концентрат із наступним складом:
- Au – 89 г/т;
- As – 13,0 %;
- Sсульф. – 20,32 %;
- FeO – 1,43 %;
- Fe₂O₃ – 32,11 %;
- Al₂O₃ – 8,0 %;
- SiO₂ – 23,8 %;
- TiO₂ – 1,34 %.
Спроби розділити цей концентрат без попередньої обробки в апараті вихрового шару не дали обнадійливих результатів.
Під час флотації в лужному середовищі з використанням вапна і мідного купоросу в найкращому випадку вміст миш’яку в піритному продукті знижується з 12-13% до 5% при вилученні його в миш’яковий концентрат на рівні 35%. Відсутність хорошого результату пояснюється фізичною та хімічною стійкістю сульфідних золото-миш’якових руд, у яких ультратонкі частинки золота дисперговані в сульфідних мінералах, представлених переважно піритом і арсенопіритом.
Тому подальше флотаційне розділення проводилося після попередньої обробки концентрату в апараті вихрового шару. 200 г концентрату після обробки в робочій камері апарату вихрового шару (маса феромагнітних частинок становила 30 г) одразу подавали у флотаційну машину та флотували за допомогою бутилового ксантогенату (50 г/т).
Рисунок 1 – Вплив тривалості обробки концентрату в АВС на технологічні показники селективної флотації: 1 – вміст миш’яку в піритному концентраті; вилучення миш’яку (2) та золота (3) у миш’яковий концентрат.
Отримані дані свідчать про те, що вміст миш’яку в піритному продукті знижується за час обробки до 10-11 хвилин із 16% до 4%. У миш’яковий концентрат, вихід якого становить близько 62%, вилучається 89-90% As і 90-91% Au при вмісті 23-24% і 125-130 г/т відповідно.
При обробці різних матеріалів в апаратах вихрового шару одним із важливих факторів, що визначають ефективність процесу, є кількість оброблюваного матеріалу, що припадає на одиницю маси феромагнітних частинок.
Недостатня кількість диполів у зоні реакції не забезпечує інтенсивного перемішування матеріалу й необхідного впливу на мінеральну поверхню. Надмірне завантаження феромагнітних частинок також негативно впливає на подальший поділ мінералів.
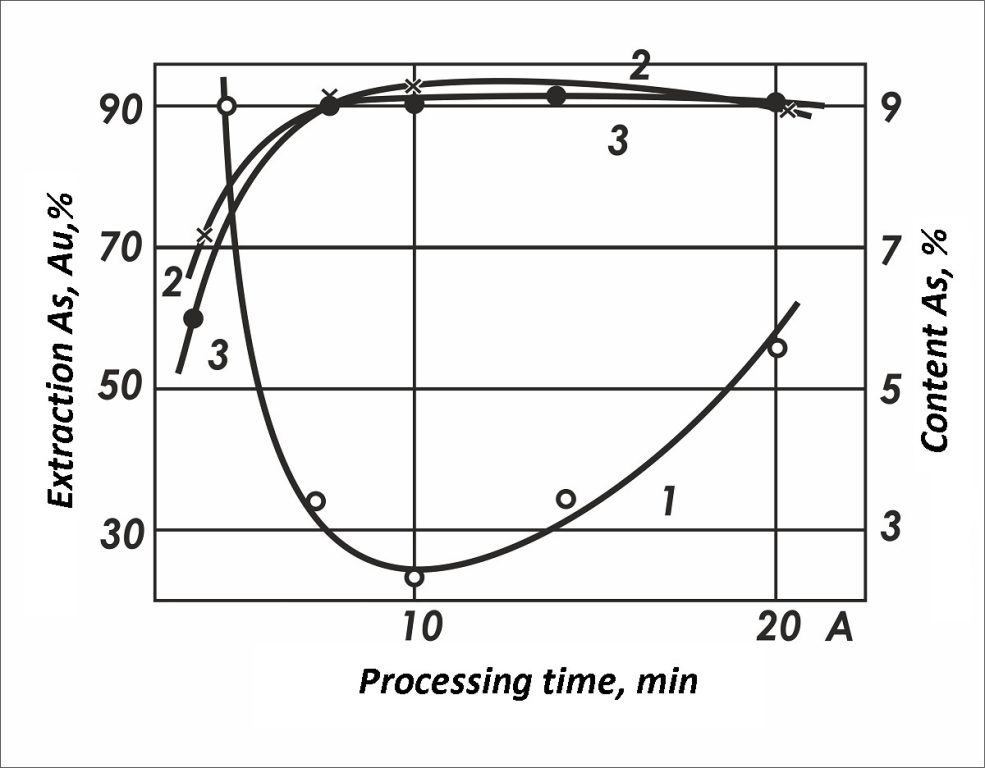
Дослідження показують, що в замкнутій системі оптимальне співвідношення маси концентрату до маси феромагнітних частинок лежить у межах 8-12. Попередня обробка концентрату при співвідношенні 10 і подальша флотація забезпечують отримання піритного концентрату з вмістом миш’яку 2,4% при вилученні миш’яку в піритний концентрат на рівні 5-5,5%.
Концентрація іонів водню в пульпі в межах рН = 5,5-10,5 не впливає на результати флотації. Під час флотації в сірчанокислому та вапняному середовищах вилучення арсенопіриту в миш’яковий концентрат у широкому діапазоні становить 94-95%, і лише в сильно лужному середовищі (рН > 10,5) спостерігається незначна депресія арсенопіриту.
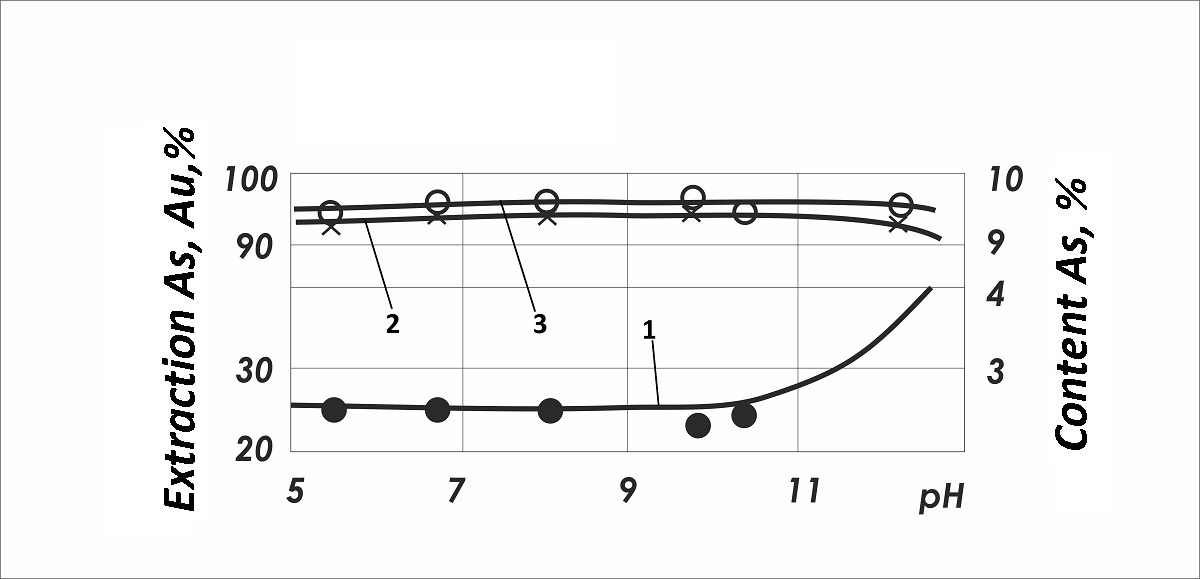
У процесі обробки концентрату в АВС на поверхню мінералів, покриту плівкою ксантогенату, впливає комплекс факторів (індукційні струми, електричні розряди, локальне підвищення тиску, підвищення температури, абразивна дія тощо), внаслідок чого колектор десорбується з мінералів і частково розкладається.
Разом із тим, після обробки в пульпі залишається частина колектора, здатного повторно сорбуватися на поверхні мінералів і негативно впливати на подальшу селективну флотацію. Додавання активованого вугілля (до 1 кг/т) у процесі обробки концентрату в АВС покращує показники.
Отриманий піритний концентрат містить 1,7-1,8% As, що дозволяє переробляти його на мідеплавильному заводі. Миш’яковий концентрат містить 26-27% As, 130 г/т Au при вилученні 95-95,5% і 92-93% відповідно.
Таким чином, короткотривала обробка золото-миш’яково-піритових концентратів в апараті вихрового шару значно покращує результати подальшої селективної флотації та забезпечує стабільне отримання багатого на золото миш’якового концентрату. При цьому апарати вихрового шару відрізняються від класичних млинів низьким енергоспоживанням (споживана потужність одного апарата не перевищує 9,5 кВт), компактними розмірами та простотою обслуговування. Тому виробництво золота з їхньою допомогою є перспективним напрямком.
Для отримання додаткової інформації щодо виробництва золота з використанням апаратів вихрового шару зверніться до наших спеціалістів за контактами, вказаними у відповідному розділі сайту.